Analyser® – the revolutionary software solution for robust products and stable processes
Does your manufacturing or development team also face these challenges?
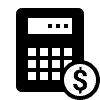
Increased costs for failures, rework and warranty
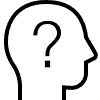
The causes of failure and warranty risks are not recognized, measures are in vain
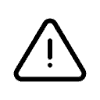
Failures in development, series start-up and production are not recognized (quickly enough)
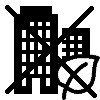
Rejects lead to increased resource, material and energy consumption
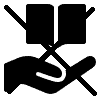
Cost-intensive production stops & non-transparent corporate knowledge
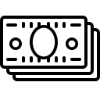
Manufacturing costs are too high for competitiveness
Our solutions for you
The Analyser® is a fully automated AI software and ensures failure-free, robust products and stable processes.
It is used across industries for development, production and assembly and processes all product validation and process curves, as well as individual values from sensor data.
Find the right solution:
The digital Production Assistant
The Curve Module
The Analyser® automatically detects failures and causes in real time and then provides solutions and measures for defective products and processes. The employee in the factory – for example in the event of a faulty screw fitting or pressing – is able to take the measures suggested by the AI system in a targeted way. Because the Analyser® reports the failure type, its causes and the associated measures to the employee within seconds.
In addition, it also contains a self-learning module so that successful measures can be reported back. This feedback is taken into account in further analyzes. Thus, the analysis of the AI-Analyser is constantly being improved with the help of employees and experts (closed loop for lessons learned).
The advantages at a glance
![]() |
![]() |
![]() |
![]() |
Quick and targeted measures instead of costly production stops |
Support of employees in real time |
Reduction of reject, failure and rework costs, as well as warranty risks |
Support in process parameterization for product start-ups & prototypes |
Analyze causes of costs and quality problems
The Transfer Function Module
However, it happens sometimes that even experts are at a loss and cannot (partly) identify the causes of failures, reworking, as well as quality and warranty issues. The problem here is the lack of knowledge about cause-effect relationships and especially their interactions within components, assemblies and manufacturing processes. The Analyser® expands knowledge by uncovering unknown cause-effect relationships and storing them in transfer functions. The transfer function now contains all important influencing variables and their effects on the product or the process.
Now all product and process parameters can be controlled so that the quality characteristics are achieved sustainably. By knowing the cause-effect relationships, the manufacturing costs can be reduced by opening too narrow tolerances of the component and production parameters. The Analyser® transfer function even provides a prediction model – so failures can be identified and eliminated before they occur. The Analyser® is therefore used for Predictive Analytics and Predictive Maintenance topics.
The advantages at a glance
![]() |
![]() |
![]() |
![]() |
Increased efficiency in resources, materials and energy |
Reduction of product manufacturing costs by opening |
Reduction of reject, failure and rework costs, as well as warranty risks |
Securing development and series start-up |
Please do not hesitate to contact us
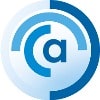
Further information
Would you like to find out more about the Analyser®? Simply register using our contact form and request our free info webinar. Click here for webinar registration
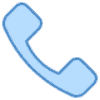
Do you have any questions?
Simply arrange a free phone call with our experts. Then we can address your needs and discuss questions more specifically. Arrange an appointment now
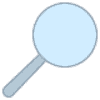
We uncover your cause-effect relationships
We offer you the opportunity to determine your unknown cause-effect relationships with the relevant influencing variables for your products and processes free of charge. Simply fill out our contact form and request a trial run.
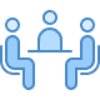
Our workshop day
We support you in your digitization project: We determine your first multiple prediction models so that you can actively control your influencing variables for sustainable quality and cost reduction.
Why Analyser®?
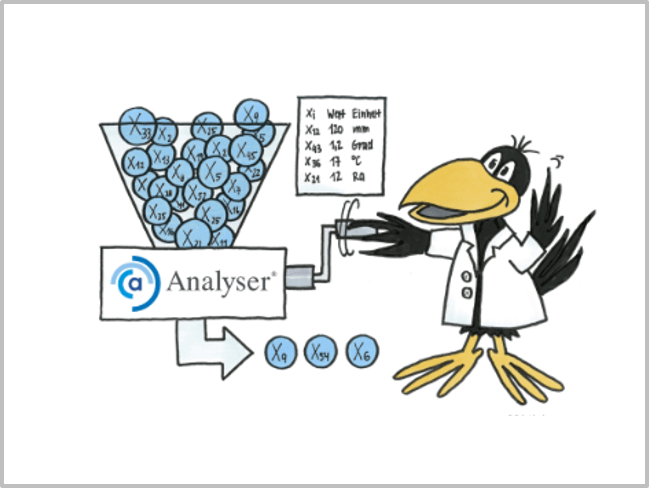
Automated modelling and sampling
This function enables employees without the knowledge of a data analyst / scientist to form the required prediction models (including sampling) in order to determine and regulate the product and process parameters for sustainable quality.

Patented AI algorithm for failure detection
Thanks to our patented algorithm, failure types are precisely identified based on curve characteristics and the corresponding causes and measures are determined consistently.
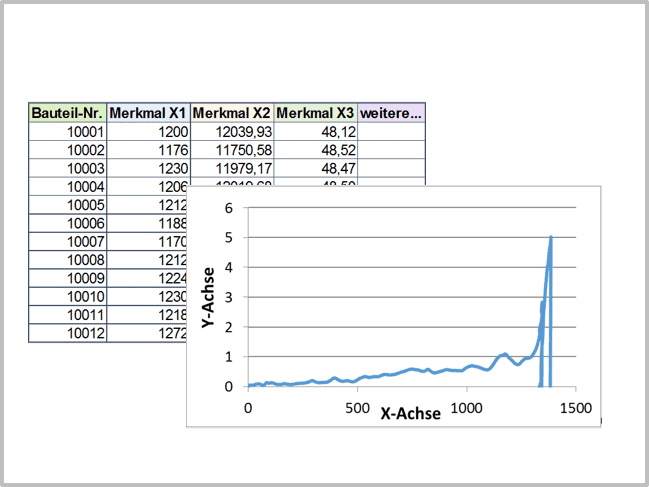
Processing of single values AND curves for the prediction model
Up until now, only with our method has it been possible to process curve characteristics as influencing variables for the prediction models. Only in this way the influencing variables on the process or the product can be precisely determined. Because the root cause is often in the curve itself and is insufficiently explained with a single value.
FAQ - Analyser®
- Which algorithm is behind the Analyser®?
The process is based on a special combination of statistical methods, (parameter) models and the unique, patented algorithm.
This allows to analyze product validation and process curves as well as individual values for robust products and stable processes. Without this patented process, it has not been possible to analyze curve characteristics fully automatically in order to identify failure types reliably. For this purpose, curve characteristics are also processed as influencing variables for the predictive models (for predictive analytics / predictive maintenance). Only in this way the influencing variables on the process or the product can be precisely determined, because the root cause is often in the curve itself and is insufficiently explained with a single value.
- Do you work with Big Data analyzes?
No, we work with samples from a large amount of data. The sample is drawn from Big Data. How the sample is drawn is part of our method from 14 years of engineering and Six Sigma experience in over 1000 projects.
- How is the Analyser® implemented?
All implementation steps for the Production Assistant and Transfer Function Module can be found here
- What is the network scheme for an implementation?
The Analyser® requires two virtual machines:
- The Analyser® server with an SQL database on Windows 10
- If there is no MES or process data management system: The IPM 6.0 server and XLM interface server with an Oracle database on Linux (IPM is a process data management system from our partner CSP. You can find more information about our partner under Cooperation)
- How should my data be available?
- Sensor data
- The data must be labeled for a successful analysis
We help you to determine the relevant influencing variables and make them measurable. We also support you with the necessary measurement system analyzes for further digitization.
- Where is the Artificial Intelligence of the Analyser®?
After a teach-in phase, the Analyser® is able to recognize failures and corresponding failure types independently. In addition, the AI system also contains a self-learning module in which successful measures are reported. This feedback is then taken into account for further analyzes. With the help of the employees and experts, the analytical ability of the Analyser® is continuously developed and improved.
Our information material
- Short description Analyser®: Analyser Short Description
- Performance description Analyser®: Analyser Performance Description
Cooperation
CSP
Software developers and software consultants for high-quality and individual solutions for quality assurance in the manufacturing industry and for database archiving.
The cooperation with our partner CSP is based on IPM® – an integrated process data management system that records all measurement and process data regardless of the manufacturer and, together with our Analyser®, detects failures in the production process at an early stage and thus ensures high quality requirements.
If there are any problems, the system alerts you in real time. So you can intervene immediately, improve the quality of your products sustainably and protect yourself reliably against product recalls or damage to your image. IPM collects all process data, such as torque or press-fit values, in a maintenance history file and guarantees access even after years if you need this information for legislature or company guidelines. www.csp-sw.de/en
Visual-XSel
The complete tool for data analysis and methods based on Six Sigma. No other program combines statistics with all important methods such as system analysis, fault tree analysis, DoE, Weibull, Shainin and Six Sigma.
Visual-XSel is connected to the Analyser® and thus part of the Analyser® process data management package. Visual-XSel is used for the modelling: The relevant influencing variables with and without interaction that determine the product functionalities and processes in the best possible way are automatically analyzed for the cause-effect relationships. www.crgraph.com
You are currently viewing a placeholder content from Google Maps. To access the actual content, click the button below. Please note that doing so will share data with third-party providers. More Information
Phone: +49 (0) 8141-88 84 03-0
Email: info@mts-contech.com
Or just fill out the contact form.