Körperschallschwingungen sind besonders im Automobilbau eine große Herausforderung. Das KI-System Analyser® bewährte sich bei der Produkt- und Prozessoptimierung.
Die Kundenbeschwerden häuften sich: „Bei bestimmten Geschwindigkeiten pfeift oder jault das Getriebe meines Autos – das nervt.“ Dieses Phänomen trat jedoch nur bei einigen Seriennummern des neuen Modells auf. Daraufhin engagierte der Automobilhersteller die Contech Software & Engineering GmbH, um Abhilfe zu schaffen. Mit Hilfe von Robust Design und dem KI-System Analyser® war es möglich, binnen weniger Wochen diese Aufgabe kostengünstig, dauerhaft und nachhaltig zu lösen.
Robust Design für Produkte und Prozesse ist eine über 14 Jahren aus Lean Six Sigma von Dipl.-Ing. Frank Thurner weiterentwickelte Methode, um robuste Produkte und stabile Prozesse zu gewährleisten. Sie erarbeitet systematisch Schritt für Schritt die gesamten funktionalen Ketten des Produktes sowie die (Herstell-)Prozessketten in acht Hauptschritten. Diese Methode bewährte sich unter anderem beim (Re-)Design von Antriebssträngen, wie sie beispielsweise beim Autobau oder in Werkzeugmaschinen verwendet werden.
Projektziele
Die (Re-)Designziele von Antriebssträngen lauten generell:
- NVH (Noise Vibration Harshness = Körperschallschwingungen) identifizieren, soweit möglich präventiv vermeiden oder zumindest deutlich verringern
- Prüfzeiten an den EoL-Prüfständen verkürzen (EoL = End of Line)
- Kundenreklamationen und Gewährleistungsrisiken vermeiden oder drastisch verringern
Im Rahmen eines Projekts für einen großen Automobilhersteller sollte die mts Consulting & Engineering mit dem Analyser® der Contech Software & Engineering GmbH für eine gleichbleibend hohe Qualität bezüglich der Akustik von Antriebssträngen sorgen.
Umsetzung
Mit der von Dipl.-Ing. Frank Thurner, dem Inhaber von Contech Software & Engineering GmbH, entwickelten Methode Robust Design erarbeitete Contech systematisch und Schritt für Schritt die gesamten funktionalen Ketten des Produktes sowie die (Herstell-)Prozessketten in acht Hauptschritten:
- Problemstellung erarbeiten
Im ersten Schritt erfolgte eine exakte Definition der Projektziele und die Zusammenstellung des Projektteams.
Zu den Zielen zählte die Minimierung der Schwingungsanregung durch Optimieren der Mikrogeometrie des Antriebs, wobei damit direkte Schwingungen und Schallabstrahlung sowie die Körperschallübertragung minimiert wurden. Dadurch sollte ein schwingungsarmer Antrieb erreicht werden, verkürzte Prüfzeiten und deutlich weniger Kundenreklamationen. Die bestätigte Mikrogeometrie dabei zu einem neuen Toleranzsetting für alle relevanten Mikrogeometrie-Merkmale führen. Dieses neue Toleranzsetting wiederum sollte durchschnittlich 30 % geringere Herstellkosten ermöglichen.
Um diese Ergebnisse nachhaltig zu sichern, galt es, Transferfunktionen für die relevanten Anforderungen (Schwingungen vermeiden, Transferpfade dämpfen, etc.) zu definieren, die relevanten Herstellparameter herauszufinden und einen Kontrollplan aufzustellen.
Das Projektteam stellte die erforderliche Kapazität vor allem durch Mitarbeiter der Contech über die Projektlaufzeit sicher. Es bestand aus dem Projektleiter, einem Akustik-Fachmann und Mitarbeiter für Versuch, Berechnung und Produktion.
- Problemstellung in messbare Größen überführen
Das Projektteam hat die wichtigsten Anforderungen zunächst identifiziert und gewichtet. Bei dem Paarweisen Vergleich legte das Team drei Zustände zugrunde:
0 = weniger wichtig als
1 = gleich wichtig
2 = wichtiger als
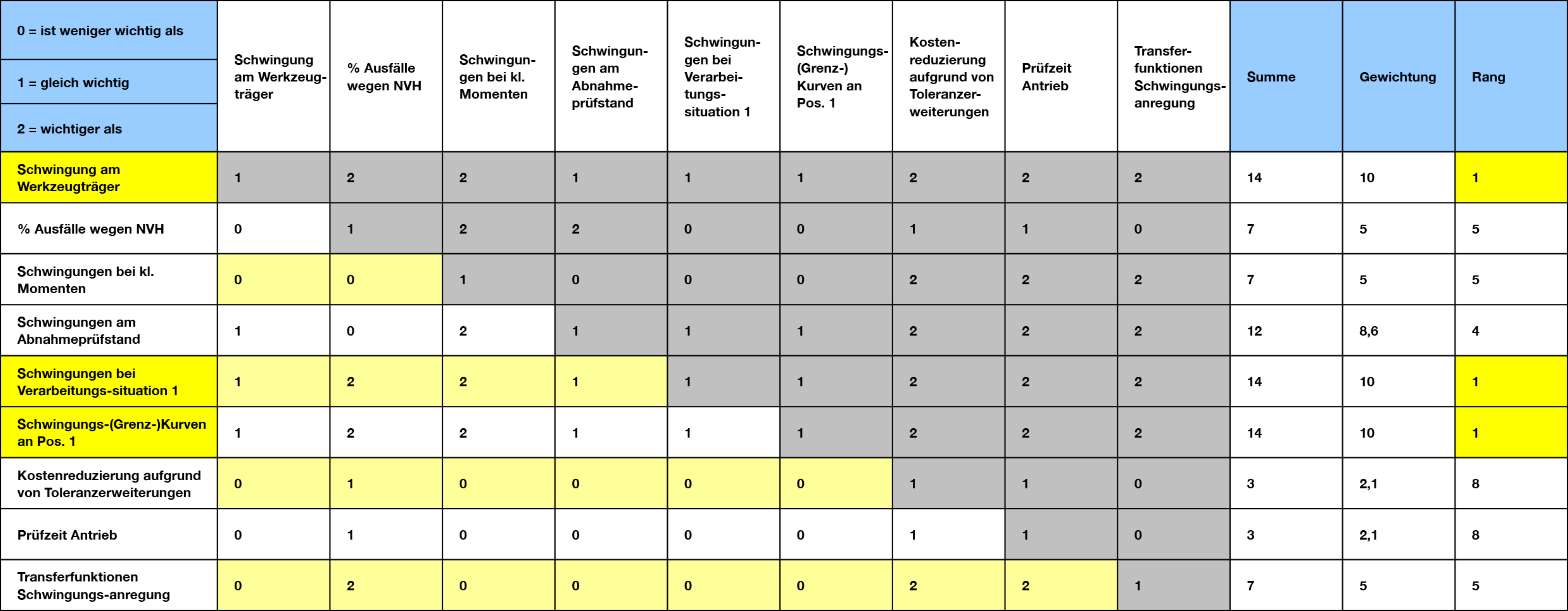
Im Paarweisen Vergleich wird die Priorität der relevanten Anforderungen ermittelt.
- Erarbeiten und priorisieren der wesentlichen Einflussgrößen für die relevanten Anforderungen
Im nächsten Arbeitsschritt widmete sich das Projektteam den Einflussgrößen Xi. Die kausalen Ketten für Produkte und Herstellprozesse galt es zu bestimmen und die technische Bedeutung der Einflussgrößen Xi für die messbaren Anforderungen Yn herauszufinden. Die Einflussgrößen Xi fasste das Projektteam in einer QFD-Matrix (QFD = Quality Function Deployment) zusammen.
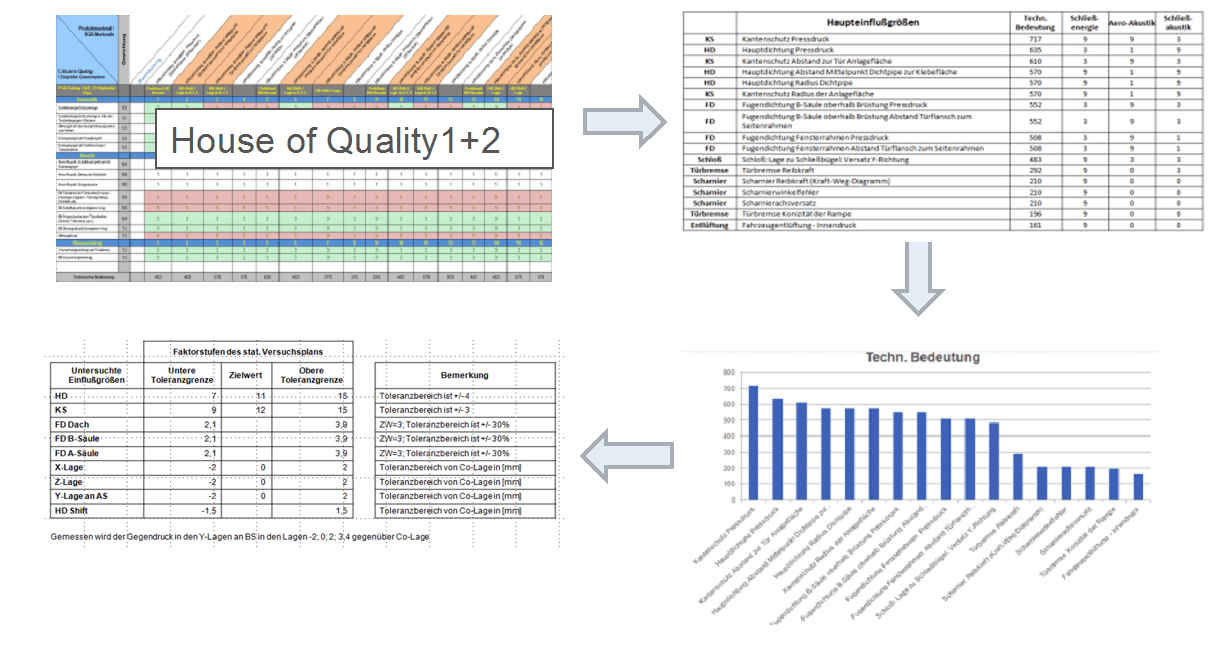
Die Konzentration auf die Haupteinflussgrößen und deren technische Bedeutung ermöglicht gezielte Versuchsreihen oder die Analyse von historischen Daten.
- Fehlermöglichkeits- und -einflussanalyse
Um weitere mögliche Fehlerquellen herauszufinden und zu gewichten, nahm sich das Projektteam die Design-FMEAs (D-FMEA = Design Failure Mode and Effectiveness Analysis) für Baugruppen und Komponenten des gesamten Antriebs vor.
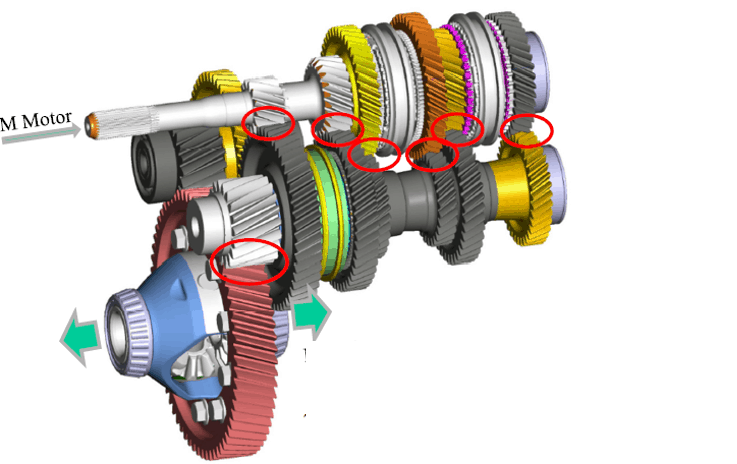
D-FMEAs für den gesamten Antrieb. Die Risikozahl wird durch die D-FMEA ermittelt.
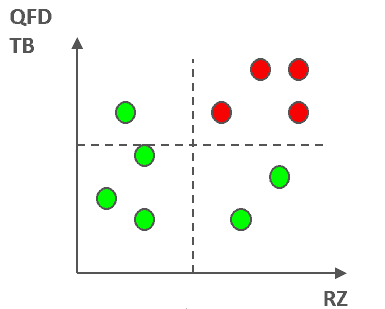
Die D-FMEA ermittelt die Risikozahl RZ = A x B (aus Auftretenswahrscheinlichkeit A und der Bedeutung B) und priorisiert somit die Einflussgrößen Xi. Zusammen mit der technischen Bedeutung aus der QFD wird eine zweidimensionale Priorisierung möglich.
- Versuche und Feldtests
Die DoE (Design of Experiments) gewährleistete, dass die durchzuführenden Versuche und Feldtests zu den gewünschten Ergebnissen führen. Dabei kamen unterschiedliche DoE-Methoden und statistische Schwarz-Weiß-Vergleiche zum Einsatz.

Versuchsplanung für Daten aus der laufenden Produktion bzw. der Vorserie oder Nullserie.
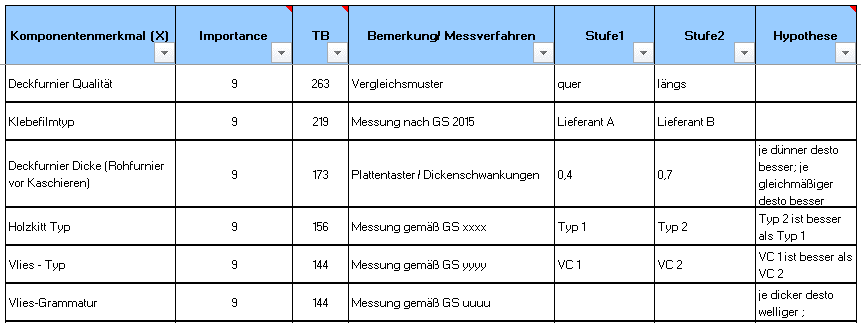
Versuche und DoE.
- Ermittlung komplexer Wirkzusammenhänge
Die Wirkzusammenhänge ermittelte das Projektteam mittels statistischer Analyse Yn = f (Xi) mit dem Analyser®.
Als Ergebnis berechnete der Analyser® die kompletten Wirkzusammenhänge zwischen NVH und der verursachenden Bauteilgeometrie.
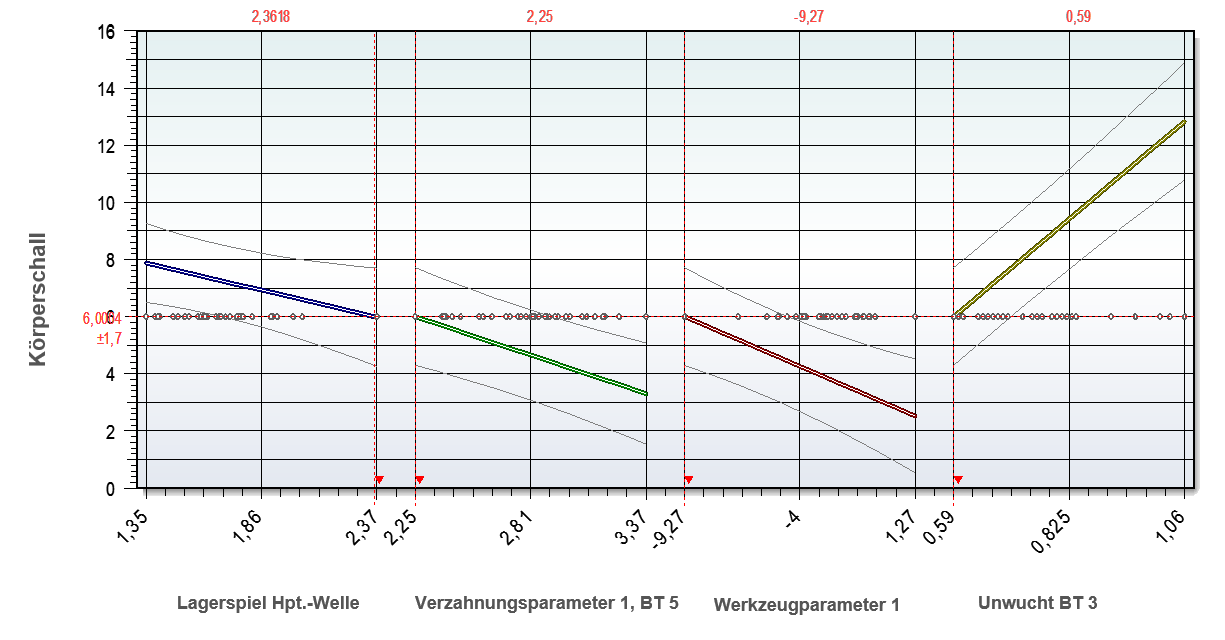
Wirkzusammenhänge zwischen Lagerspiel der Hauptwelle, Verzahnung, Werkzeug und Unwucht.
- Einflussgrößen prüfen und gewichten
Um Over-Engineering zu vermeiden, erfolgte eine statistisch abgesicherte Parametrierung und statistische Tolerierung von Produktmerkmalen und Prozessparametern. Dazu verifizierte das Projektteam die Einflussgrößen Xi und optimierte sie, parametrisierte die Produkt- und Prozess-Parameter und nahm eine Monte-Carlo-Simulation vor.

Zusammenfassung für normierte Körperschallwerte: Vermeiden von Over-Engineering durch statistisch abgesicherte Parametrierung und statistische Tolerierung von Produktmerkmalen und Prozessparametern.
- Statistische Erfolgskontrolle
Abschließend erfolgte eine Statistische Prozesskontrolle (SPC) für die relevanten Produktmerkmale und Prozessparameter.

SPC sichert die mit Analyser gewonnenen Erkenntnisse nachhaltig ab.
Ergebnisse
Der Kunde konnte aufgrund der Analyseergebnisse und der Handlungsempfehlungen seine Antriebsstränge so konstruieren, dass seit den Design-Änderungen keinerlei einschlägige Kundenreklamationen aufgrund von Akkustik- und Geräuschthemen auftraten. Darüber hinaus reduzierte der Kunde die EoL-Akkustikfehler von rund 12 auf unter 0,5%. Damit gingen die Nacharbeitskosten auf einen zu vernachlässigenden Betrag zurück. Aufgrund der Vermeidung von Over-Engineering war es zudem möglich, die Herstellkosten um 30% zu senken. Das Projektteam hat validierte KPIs aus den Prozess- und Vorserien an die Serienprozess-Verantwortlichen dokumentiert übergeben. Mit dem Projektabschluss erfolgte die Übergabe der Herstellprozesse und ihrer Parametrierung für SPC (Scorecard 3 + 4) usw. an die Serienverantwortlichen.